Manufacturing job costing: How to get it right
According to a recent report from the Institute of Supply Management, manufacturers have mixed opinions about where profit margins are headed. Between the end of 2019 and May 2020, 67% of survey respondents predicted they'd see lower profit margins or no change.
For some manufacturers, job costing pitfalls may make a significant difference in their profit margins, despite great sales and high productivity and throughput. A failure to accurately forecast how much a job will cost, and to price it accordingly, can undercut your profits.
So where do manufacturers go wrong when it comes to job costing?
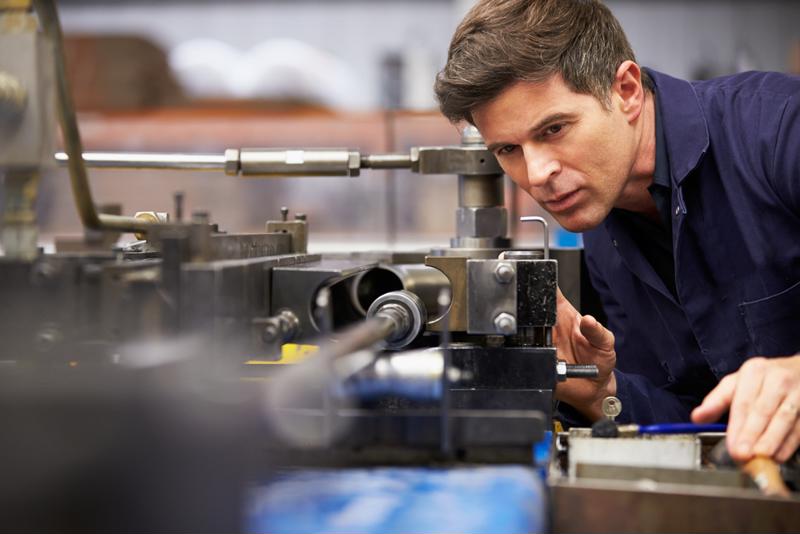
Too broad a net: Overwhelmed by data, underperforming on analysis
One of the first major pitfalls manufacturers could experience is an onslaught of irrelevant data in their job costing forecasts.
While being comprehensive is important, taking too many factors into account, including metrics that are static and inflexible, may actually hinder your decision-making abilities. While a sum total of costs that includes all indirect costs, including the most tangential, can be helpful for establishing a price, there comes a time when the manufacturer simply needs to assume some items as the cost of doing business.
To keep your business focused on actionable metrics during your job costing, stick to keeping a close eye only on the KPIs that will actually influence your decision-making. This can change as time passes, but if you're focused on improving throughput or lowering prices by changing your sourcing practices, those are the metrics you should really monitor in drilled-down reports.
Improperly attributing indirect costs
That said, keeping tabs on your indirect costs is absolutely essential to understanding job cost breakdowns, particularly for manufacturers who run multiple facilities or simultaneously produce a slate of different products.
For instance, let's assume a manufacturer makes two different products and uses a dedicated facility for each. Obviously, most operations don't break down so simplistically, and in reality, sharing overhead resources can be a great cost-saving strategy. That said, there's something important to note here.
Namely, your indirect costs do not apply evenly across your facilities or the products you produce.
To go back to our example, let's suppose that one product needs to be created in a facility that's close to a specific source material. That facility may cost more to run and maintain than your other facilities due to its remote location. If that's the case, the product that is created in that facility requires a disproportionate amount of indirect costs compared to the products that are produced in cheaper facilities.
Accurate job costing relies on your ability to allocate overhead costs appropriately.
Outdated job costing processes
One monumental risk for manufacturers when it comes to job costing is using outdated manual processes to calculate their costs and margins.
This is risky for two main reasons. First, it introduces a greater chance for human error than automated calculations. Second, it's susceptible to relying on siloed information. If you have an incomplete level of access, you'll undervalue the product, and you won't account for the indirect costs mentioned above.
Learn more about manufacturing job costing, and find out how state-of-the-art ERP systems and implementation can help enhance the process.